JÓZEF MAKOWSKI brygadzista działu głównego mechanika w Łukowskiej Fabryce Obuwia twierdzi, że potrzeba jest matką wynalazków.
Z tekj potrzeby narodziło się jego 15 wniosków racjonalizatorskich w ciągu ostatniego pięciolecia, nie licząc wcześniejszych, które opracował w fabryce, pracując tu od początku i tych pierwszych – w zakładach remontu maszyn w Cieplicach Śląskich, gdzie tego chłopa z podłukowskiej wsi zagnała chęć pracy w przemyśle. Ukończył zaledwie 7 klas szkoły podstawowej, ale smykałkę do mechaniki miał od dziecka, a literatura fachowa, w której rozczytuje się wieczorami wiele mu ułatwiła. Nawet prototypy swoich usprawnień potrafi wykonać sam z 3 pracownikami brygady. Pracują nad tym wieczorami, bo wtedy – jak mówi – nikt nie przeszkadza, i żadne ciekawe oczy nie zapeszą roboty.
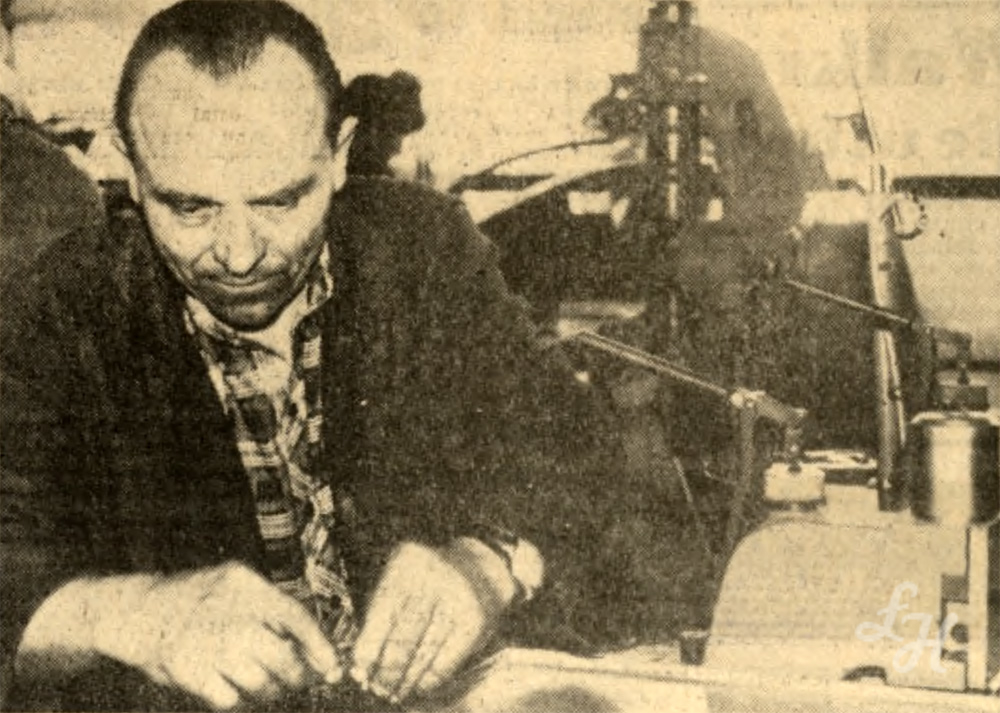
Zasłużony racjonalizator i brygadzista Józef Makowski tylko na chwilę oderwał się od swojej maszyny, by opowiedzieć, jak rodzą się jego pomysły. ( fot. B. Biernat )
– Który z moich pomysłów wspominam, jako najtrudniejszy i najbardziej pracowyty? – Makowski zastanawia się chwilę. – Wszystkie nie były łatwe. Ale tak, oczywiście – ścieraczka do pasa. Trzeba było zrobić coś, czego nie było nie tylko w zakładzie, lecz w ogóle w Polsce.
Przemysł nie produkował takich maszyn do obuwia klejonego. Patrzyłem, jak pracowite są operacje ręczne, jak nad wykonaniem jednego wzoru mozoli się dziesięć osób. A tu wkrótce nasz zakład miał rozpocząć produkcję seryjną butów klejonych. Wziąłem się do roboty, ślęczałem nad wykonaniem tej maszyny cały miesiąc, ale się udało. Maszyna gotowa była dosłownie pięć minut przed rozpoczęciem produkcji.
Józef Makowski posiada odznakę zasłużonego racjonalizatora produkcji. Najświeższym jego pomysłem jest tzw. krążkowacz do nitowania krążków w cholewkach, i do tej operacji fabryka nie miała maszyny, nitowanie odbywało się ręcznie. Urządzenie Makowskiego pozwoliło zastąpić pracę 4 osób, przy czym operacja jest o wiele lżejsza, bo zmechanizowana. Prototyp rodził się dwa tygodnie. Oczywiście i nad tym pracowała solidarnie cała brygada.
* * *
Z HENRYKA BOROWCA, młodziutkiego, świeżo upieczonego inżyniera w dziale gł. mechanika dumni są w fabryce łukowskiej. Taki młody, jeszcze był na stażu, a już interesował się pomysłami racjonalizatorskimi – mówią. Szczególnie wdzięczne mu są kobiety, zatrudnione przy smarowaniu klejem elementów obuwia. – Jemu zawdzięczamy znacznie lepsze warunki pracy. Bo nasz inżynier zaczął próbować swoich racjonalizatorskich umiejętności od poprawy warunków bhp.
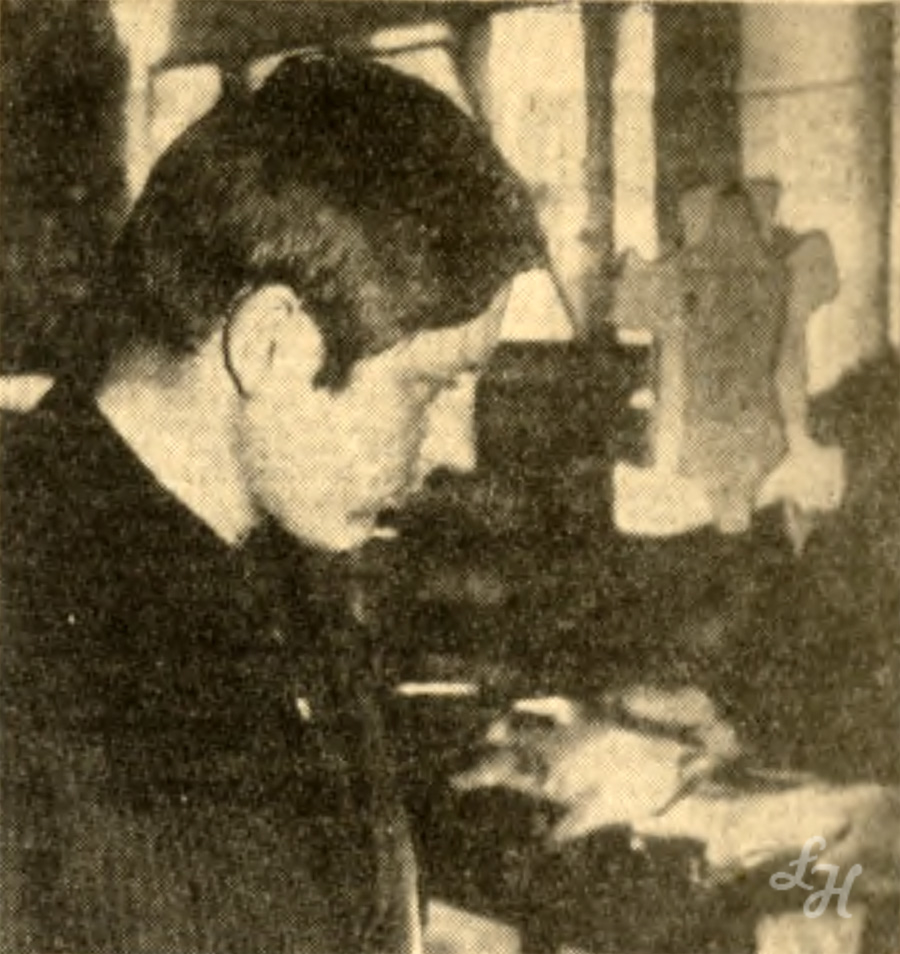
Przedstawiciel młodego pokolenia inż. Henryk Borowiec przy stole z wyciągiem, skonstruowanym według jego pomysłu. ( fot. B. Biernat )
Najpierw zainteresowały go ciężkie regały, zwane popularnie reklami, na których przesuwa się przez całą halę elementy butów. Regały miały kółka nie dostosowane do dużych ciężarów. Przesunięcie rekla wymagało więc dużo wysiłku, a wózka motorowego w zakładzie ani na lekarstwo. Inżynier przekonstruował kółka, umieszczając w nich nowe łożyska. Teraz znacznie lżej ciągnąć ten ciężar, ale inż. Borowiec jeszcze nie jest zadowolony. Mówi że musi popracować nad dalszym usprawnieniem.
Potem przyszła kolej na owo klejenie. Klej jak wiadomo, zawiera właściwości toksyczne. Dla zmniejszenia szkodliwych oparów nad każdym stanowiskiem w hali umieszczono wyciągi, połączone całym systemem rur. Nie było to wygodne, ani bezpieczne. Każde wstanie od stołu groziło stłuczeniem głowy, a rury którymi obudowana była hala, też przeszkadzały w swobodnym poruszaniu się. Młody racjonalizator skonstruował zupełnie nowy stół z małym wyciągiem wmontowanym w bok blatu. Działa on lepiej od starego, nie ogranicza swobody ruchów. W tej chwili wykonano już 30 stołów według pomysłu inż. Borowca. Kobiety bardzo sobie chwalą ten warsztat pracy i życzą młodemu racjonalizatorowi, który właśnie niedawno skończył staż, by jego dalsze lata pracy w fabryce łukowskiej były równie owocne.
Spośród 33 projektów będących efektem pomysłów pracowników łukowskiej fabryki , które przyniosły w ub. roku 735 tys. zł oszczędności, nie mówiąc o korzyściach niewymiernych w postaci poprawy warunków pracy, warto wspomnieć o wniosku popularnej w zakładzie trójcy: kierownika produkcji Filarskiego oraz dwóch majstrów: Antoniaka i Pietrasia. Pomysł ten, którego efekty oblicza się na 480 tys. zł dotyczy konstrukcji obcasa, zapewniającej prawidłową stójkę trzewika. A więc buty będę ładniejsze, wygodniejsze, klient nie będzie narzekał.
Autor: H. Chabros
Źródło: “Kurier Lubelski” R.15, nr 101, 30 kwietnia – 1 maja 1971 r.
Dodaj komentarz